Posted by Zosi Team
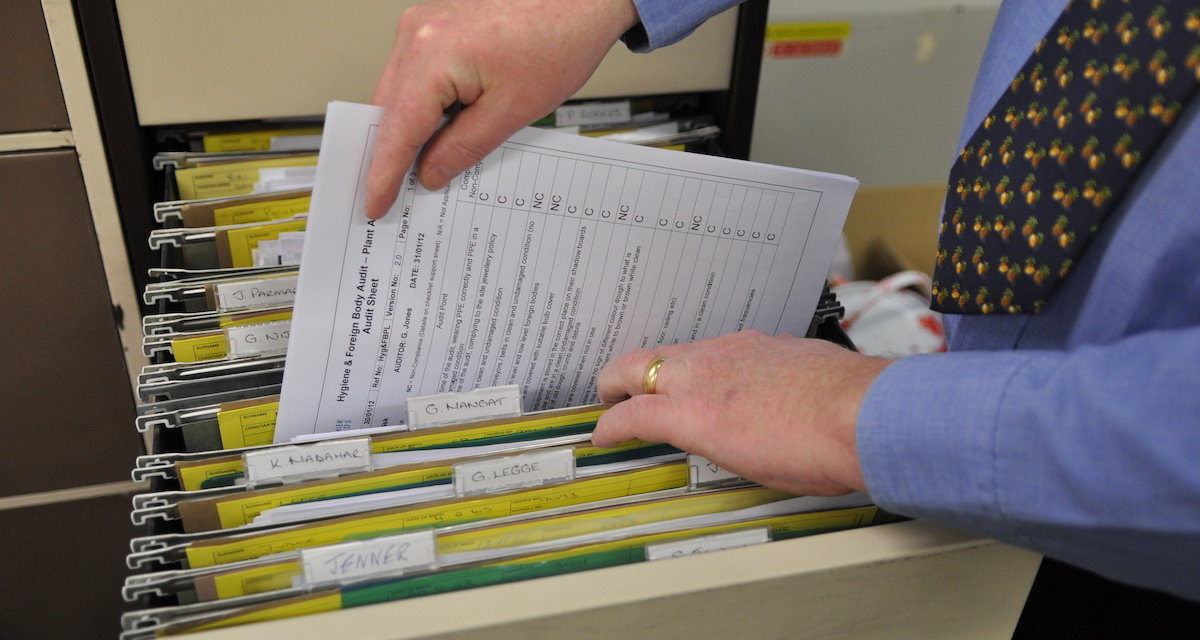
When preparing for external audits, the best preparation is your internal audit system. While many non-conformances may seem out of your control, you can easily manage the documentation behind your internal audit system and strengthen your results.
Of course, your process is dependent upon your facility, but some documentation practices are better than others. Explore different methods and weigh the pros and cons to determine which is best for you.
Performing an internal audit might seem like a daunting task, so many companies resort to the walk-through method. Simply walking through your facility and performing a visual inspection of processes as they occur is one way to verify that your processes and employees are performing as expected. While this is considered a valid method to many facilities, it is not always sufficient to supporting a third-party audit process. Lack of documentation of what you observe in addition to inconsistency of observation can lead to a non-conformance when it does come time for your third-party audit.
Preventing Audit Non-Conformances with Good Documentation
More detailed than the walk-through method is the GFSI System Checklist. By having a clear outline of procedures, people, product, and facilities that you are observing, you reduce the chance of missing abnormalities within your system. If your facility is covered by SQF, BRC, or FSSC 22,000, the GFSI System Checklist details line-by-line what you need to verify. Furthermore, when you do identify non-conformances in your internal audit, create a Corrective Action Register. Identify where you have an issue, what action was taken to correct the issue, and how you will prevent any recurrence in the future.
As you inspect your facility, be sure to record the details of your internal audit process. Have representatives from operations, quality assurance, and maintenance present to ensure that every point of view is addressed. It is even more beneficial to include someone from sanitation, as well. When going through the checklist, you may also need to review written programs before continuing when you approach certain line items.
Customized Checklists
An even more effective method for established facilities is customized checklists for your specific facility, which can be used for plant inspections or specific processes. Customized checklists guide the auditor through each step you take to secure your facility’s internal audit. It ensures all elements of the checklist are completed, because you can be as detailed as necessary to verify that each point in your production process is audited. If additional documents need to be reviewed before completing an item, you can outline this with a customized checklist. Additionally, it reinforces audit objectives and scope. Properly define what you are trying to review in this process, setting clear designations for product, processes, people, facilities, or a combination of any of those elements.
By using customized checklists, you have a written record that provides evidence to a third-party auditor that you have adequately completed the process. As you document, be sure to include details of the process, including the date, time started and finished, duration, and team members who were present. Document specific inspection results and identify any nonconformances that you find, as well as the corrective actions to be taken. The checklist you create can be detailed or limited, depending on the experience of the auditor. With more detailed checklists, there is less room for error with less experienced internal auditors. Update the checklist as needed or as changes occur, this includes changes of product, equipment, or the facility itself. Inspection results need to be evaluated by the internal audit team and any other relevant personnel.
All checklists have their benefits and their downfalls. When using a checklist, do not let the details of the checklist drive the entire process. At times you might lose sight of something that might be otherwise obvious because you only look for the items that are defined. Use the acronym STOP—stop, think, observe, proceed—to verify that you aren’t overlooking anything in your internal audit. Stop the process at different points and evaluate what you are truly observing. Think about the requirements of the checklist and at what points you can take action. Observe the full process from beginning of manufacture through shipping; take note that employees are complying with procedures and that equipment and structure are adequate. Finally, proceed to the next step on your checklist. Once you have taken into account what you are observing and the actual requirements for an item, you can repeat the process with the next requirement on the checklist.
Conclusion
Internal audits are a necessary, but helpful, part of your external audit process. With practice and time, the process becomes more streamlined and documentation becomes a bit more natural. Keeping proper records and documentation protects your company from legal action, but more importantly acts as additional security for your consumers and your brand. Consistent training further reinforces best practices. With Zosi, you can delve into internal audit requirements with both our Basic and Advanced Internal Audit courses. Learn more by enrolling today.